Unsere Geräte werden häufig in Branchen wie Pharmazie, Chemie, Klebstoffe, Photovoltaik, Batterien, Polymermaterialien, Lotpasten, Lebensmittel, Farbstoffe, Kosmetika und Kunststoffe eingesetzt.
MEHR LESEN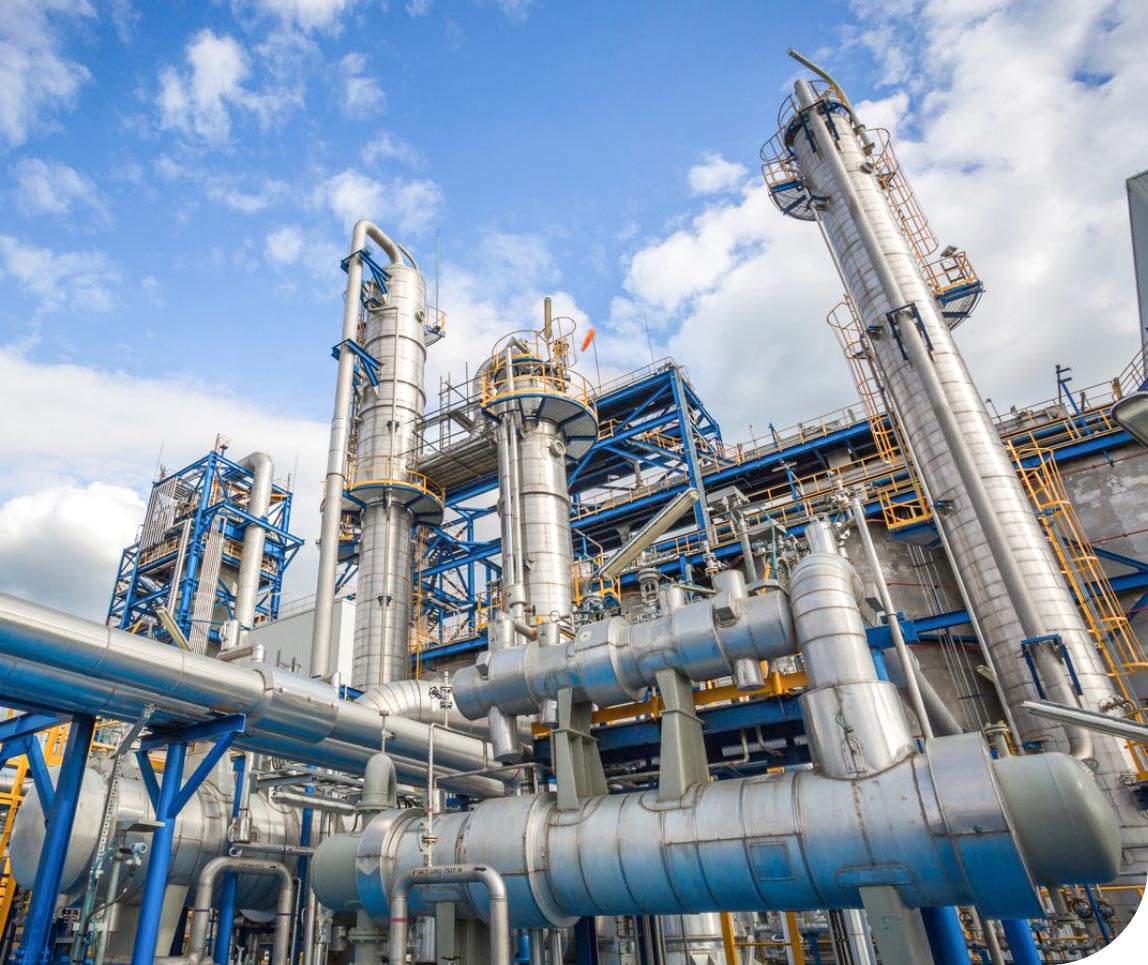
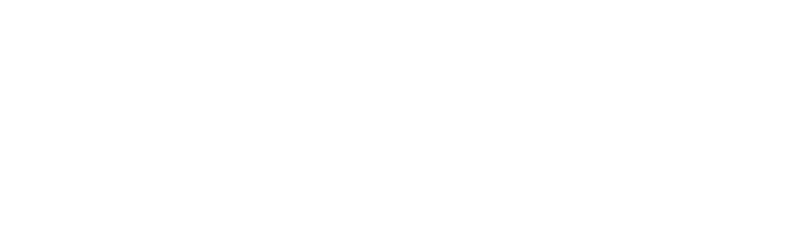
Eine ausgereifte Fabrik, auf die Sie zählen können
Gegründet
Personal
Arbeitsbereich
Exportländer
Der Standardmischer ist für die meisten Produkte mit einer Materialviskosität von unter 500.000 CP geeignet. Diese Maschine legt den Fokus auf die Zerkleinerung und Emulgierung von Materialien, um die gewünschte Homogenität des Endprodukts zu erreichen.Ein Vakuummischsystem, ein hydraulisches Hebesystem, eine zentrale Steuerung und Sicherheitseinstellungen gehören zur Standardausstattung dieses Modells. Das Gerät besteht in der Regel vollständig aus Edelstahl oder verfügt über Edelstahlkomponenten an den materialberührenden Teilen.
Der Dispergiermischer ist in erster Linie zum Mischen von körnigen Materialien konzipiert, bei denen die Anforderungen an die Partikelgröße von entscheidender Bedeutung sind und außerdem ein hoher Bedarf an Vakuumentgasung besteht. Die Wahl des Dispergierscheibendurchmessers und der Lineargeschwindigkeit der Dispergierscheibe beeinflusst diese Anforderungen maßgeblich. Typischerweise ist eine Hochgeschwindigkeits-Dispergiereinheit die Hauptkomponente, ergänzt durch andere Mischmethoden. In einigen Fällen können zwei Hochgeschwindigkeits-Dispergiereinheiten gleichzeitig verwendet werden, um die Mischeffizienz zu verbessern.
Der hochscherende Emulgierkopf des Emulgiermischers bietet je nach Materialbedarf verschiedene Optionen, wie z. B. einen offenen Statorkopf, einen Zwei-Wege-Saug-Statorkopf oder einen koaxialen Scherkopf. Die Ausrüstung kann entweder über zwei Emulgierstrukturen oder eine Kombination aus einem Emulgierkopf und anderen Mischmethoden verfügen. Um das Experimentieren zu erleichtern, erlauben wir die austauschbare Verwendung des Scheremulgierkopfs und des Hochgeschwindigkeits-Dispergierkopfs.
Um die Materialzufuhr zu vereinfachen, haben wir den traditionellen Multifunktionsmischer weiterentwickelt, der die Zugabe von Pulver ohne Öffnen der Vakuumabdeckung ermöglicht. Während des normalen Betriebs erzeugt der Hochgeschwindigkeits-Scheremulgierrotor einen Siphoneffekt, der Pulver oder Flüssigkeit direkt in das gemischte Material zieht und so Staub und Verunreinigungen vermeidet, die normalerweise beim Öffnen der Abdeckung entstehen. Diese Innovation ist ideal für anspruchsvolle Standardanwendungen wie elektronische Materialien.
Bei der Anwendung des Multifunktionsmixers haben wir einen großen Erfahrungsschatz gesammelt. Unsere Kombinationen können in Hochgeschwindigkeit und Hochgeschwindigkeit, Hochgeschwindigkeit und Niedriggeschwindigkeit oder Niedriggeschwindigkeit und Niedriggeschwindigkeit kategorisiert werden. Der Hochgeschwindigkeitsbereich umfasst Hochscher-Emulgiergeräte, Hochgeschwindigkeits-Dispergiergeräte, Hochgeschwindigkeits-Antriebsgeräte und Schmetterlingsrührgeräte. Der Abschnitt mit niedriger Geschwindigkeit umfasst Ankerrühren, Paddelrühren, Spiralrühren, Spiralbandrühren, Rechteckrühren usw. Jede Kombination bietet einen einzigartigen Mischeffekt.
In der Massenproduktion sind herkömmliche Anlagenstrukturen möglicherweise nicht mehr geeignet. Die Antriebseinheit ist typischerweise direkt am Mischbehälter befestigt. Diese Geräte fassen in der Regel mehr als 1000 Liter und das Hinzufügen eines externen Banddesigns zum Ankerblatt kann zu unerwarteten Ergebnissen führen. Bei Materialien mit etwas niedrigerer Viskosität kann auch die Installation von Leitblechen an der Tankwand die Leistung verbessern. Nantong Hennly verfügt über umfangreiche Erfahrung mit diesem Modell und kann bei der Lösung praktischer Herausforderungen helfen.
Mit zunehmender Leistung elektronischer Produkte steigt auch die von den Bauteilen erzeugte Wärme. Herkömmliche Lötmaterialien und leitfähige Materialien erfordern eine verbesserte Hochtemperaturbeständigkeit. Dadurch werden höhere Anforderungen an die Produktionsanlagen dieser Materialien gestellt. In diesem Zusammenhang hat Hennly ein Produkt entwickelt, das Temperaturen von 280 °C standhält, sich zudem schnell aufheizt und abkühlt und so die Herausforderungen komplexer Herstellungsprozesse löst. Gleichzeitig wurde die kontinuierliche Hochtemperaturbeständigkeit, Abdichtung und Langzeitbeständigkeit der Mischausrüstung überwunden und so effektiv auf die Bedenken spezifischer Sektoren in der Elektronikmaterialindustrie eingegangen.
Der Zweiwellenmischer besteht normalerweise aus einer Gruppe von Hochgeschwindigkeits- und einer Gruppe von Niedriggeschwindigkeitsmischern, die verschiedene Partikel in kurzer Zeit mischen können, um einen gleichmäßigeren Mischeffekt zu erzielen. Der Mischtyp kann entsprechend den Eigenschaften verschiedener Materialien geändert werden, um unterschiedliche Mischanforderungen zu erfüllen. Die Geräte sind einfach aufgebaut und leicht zu warten und zu reinigen. Der Zweiwellenmischer ermöglicht eine hocheffiziente Mischung und lässt sich problemlos in den Bereichen Medizin, Lebensmittel, Chemie usw. bedienen.
Ein Mischer mit hohem Drehmoment spielt eine wichtige Rolle beim Mischen thixotroper Materialien. Mischer müssen in der Regel großen Drehmomenten standhalten, um die Stabilität und Effizienz des Mischvorgangs zu gewährleisten. Daher ist die Stabilitätskonstruktion und Positionierung des Gestells der Schlüssel zur Gewährleistung eines reibungslosen Mischvorgangs der Ausrüstung. Darüber hinaus ist die Leistungsauswahl des Motors besonders wichtig, da der Mischer in der Regel über eine lange Laufzeit und hohe Belastung laufen muss. In dieser Hinsicht verfügt Hennly über umfangreiche Anwendungserfahrung.
Der Standard-Hochgeschwindigkeitsdispergierer bietet normalerweise zwei Hebeoptionen: hydraulischen Hebevorgang und pneumatischen Hebevorgang. Die Wirksamkeit von Hochgeschwindigkeit Die Dispergierung hängt von der Art und Größe der Dispergierscheibe ab. Das Verhältnis der Dispergierscheibe zum Tankdurchmesser, die Lineargeschwindigkeit der Dispergierscheibe und der Stromverbrauch der Scheibe haben alle direkten Einfluss auf die Dispergierwirkung. Nantong Hennly verfügt über umfangreiche Erfahrungen in diesem Bereich und ist bereit, dieses Wissen mit Kunden zu teilen.
Der Vakuum-Hebe- und Senk-Dispergierer ist ein neu optimiertes Produkt, das auf der Kombination eines Vakuum-Dispergierers und eines Schaber-Dispergierers basiert. Es arbeitet unter Vakuumbedingungen, wobei die Hochgeschwindigkeits-Dispergierschale gleichzeitig eine Hochgeschwindigkeits-Dispersion und eine vertikale Bewegung ausführt. Diese Konstruktion stellt sicher, dass das Material auf allen Ebenen im Behälter gründlich gemischt wird. In Kombination mit einer Schabervorrichtung werden hervorragende Dispergierergebnisse in kürzester Zeit erzielt, wodurch die Dispergierzeit deutlich verkürzt und die Gesamteffizienz gesteigert wird.
Unsere Geräte werden häufig in Branchen wie Pharmazie, Chemie, Klebstoffe, Photovoltaik, Batterien, Polymermaterialien, Lotpasten, Lebensmittel, Farbstoffe, Kosmetika und Kunststoffe eingesetzt.
MEHR LESENIndustrielle Entladungssysteme spielen eine Schlüsselrolle in der modernen industriellen Produktion. Mit den zunehmend strengen Umweltschutzbestimmungen ist die Kontrolle der Emission schädlicher Gase zu einer wichtigen Aufgabe geworden, die von Unternehmen in verschiedenen Branchen nicht vermieden werden kann. Eine effektive Abfallgasbehandlung trägt nicht nur zur Verringerung der Umweltverschmutzung bei, sondern verbessert auch das Image der sozialen Verantwortung und die Marktwettbewerbsfähigkeit von Unternehmen. Klassifizierung und Gefahren von schädlichen Komponenten im Industrieabfallgas Industrieabfallgas umfasst hauptsächlich Schwefeldioxid (So₂), Stickoxide (NOₓ), flüchtige organische Verbindungen (VOCs), Partikel (PM), Kohlenmonoxid (CO) und einige Schwermetalldämpfe. Diese Schadstoffe haben einen ernsthaften Einfluss auf die atmosphärische Umgebung und die menschliche Gesundheit. Beispielsweise sind Schwefeldioxid und Stickoxide die Hauptursachen für sauren Regen, und flüchtige organische Verbindungen sind Vorläufer der Ozonschichtabweichung und des photochemischen Smogs. Die Kontrolle der Emission dieser schädlichen Gase ist die Grundlage für die Erreichung der Luftqualitätsstandards. Überblick über die Technologie zur Behandlung von Gasbehandlung in Industrieabfällen Absorptionsmethode Das Absorptionsmethode erfasst schädliche Komponenten in Abfallgas durch flüssige Absorptionsmittel, was eine gemeinsame Methode zur Kontrolle von Säuregasen wie So₂ ist. Das FAD-Gas-Desulfurization-System (FGD) verwendet Kalksteinschlamm, um Schwefeldioxid zu absorbieren, und reagieren, um Gips zu erzeugen, was die Vorteile von Abfallgasbehandlung und Ressourcennutzung von Nebenprodukten hat. Adsorptionsmethode Die Adsorptionstechnologie eignet sich zur Behandlung von flüchtigen organischen Verbindungen mit niedriger Konzentration (VOC) und einigen schädlichen Gasen. Der aktivierte Kohlenstoffadsorber erfasst schädliche Komponenten im Abgas durch physikalische Adsorption und regeneriert dann den Aktivkohlenstoff durch thermische Desorption oder Dampfdesorption. Katalytische und nicht katalytische Verbrennungsmethoden Die katalytische Verbrennung reduziert die Verbrennungstemperatur schädlicher Gase durch Katalysatoren und wandelt schädliche Gase wie VOCs und CO in Kohlendioxid und Wasser um. Die nicht katalytische Verbrennung basiert auf einer Hochtemperaturoxidation, um die schädlichen Gasemissionen wirksam zu reduzieren. Plasma mit niedriger Temperatur und photokatalytischer Technologie Die aufstrebende Plasma-Technologie verwendet energiereiche Elektronen, um Abgasmoleküle zu zersetzen oder schädliche Substanzen zu transformieren. Die photokatalytische Technologie verwendet Photokatalysatoren, um schädliche Gase unter Lichtbedingungen katalytisch abzubauen, was für die Behandlung mit niedriger Konzentration geeignet ist. Schlüsselsteuerpunkte im Systemdesign Abfallgasvorbehandlung Effektive Vorbehandlungsmaßnahmen können die Lebensdauer der Behandlungsgeräte verlängern und die Effizienz der Behandlung verbessern. Beispielsweise können Staubsammler zuerst Partikel entfernen und die Last der nachfolgenden Absorptions- oder katalytischen Geräte verringern. Abgashomogenisierung und Temperatur- und Feuchtigkeitsregulation Die Gleichmäßigkeit des Abgasstroms und der Zusammensetzung ist entscheidend für den stabilen Betrieb der nachfolgenden Behandlungsgeräte. Stellen Sie sicher, dass die Abgasbedingungen rational entworfen werden, um Luftkanäle und Temperatur- und Feuchtigkeitskontrollgeräte zu entsprechen. Mehrstufige Gelenkbehandlungslösung Für komplexes Abgas wird eine multi-stufige Behandlungsprozesskombination verwendet, um eine koordinierte Kontrolle zu erreichen. Zu den gemeinsamen Kombinationen gehören die Verbrennung der Denitrifikationskatalytik der Staubentfernung, die eine Vielzahl von schädlichen Gasen wirksam abdeckt. Betriebsmanagement- und Überwachungstechnologie Online -Überwachungssystem Erstellen Sie eine vollständige Online-Überwachungsplattform, um die Echtzeitüberwachung von Schadstoffen wie So₂, Noₓ, CO und VOC zu erreichen. Durch die Datenerfassung und -analyse werden Abnormalitäten in der Zeit entdeckt, Betriebsparameter werden angepasst und die Emissionen entsprechen den Standards. Gerätewartung und regelmäßige Überholung Stellen Sie den normalen Betrieb der Abgasbehandlungsgeräte sicher, um übermäßige Emissionen aufgrund des Ausfalls aus dem Gerät zu vermeiden. Regelmäßige Reinigung von Katalysatoren, Überprüfung der Versiegelung und Kalibrierungssensoren sind grundlegende Arbeit, um den stabilen Betrieb des Systems zu gewährleisten.
2025-07-14Industrielle Hochschermischer und traditionelle Mischer sind zwei gängige Arten von Mischgeräten in der modernen industriellen Produktion. Es gibt signifikante Unterschiede zwischen den beiden in Strukturdesign, Arbeitsprinzip und Anwendungseffekt. Durch einen detaillierten Vergleich aus professioneller Sicht können wir die herausragenden Vorteile von industriellen Hochschermixern in vielen Aspekten klar verstehen und für die Benutzer für die Auswahl geeigneter Geräte eine wichtige Referenz bieten. Effiziente Scher- und Verbreitungsfähigkeiten Der industrielle Hochschertischmischer bildet eine starke Scherkraft durch Hochgeschwindigkeits-rotierende Streifer und Statoren, um eine schnelle Zerkleinerung, Dispersion und Homogenisierung von Materialien zu erreichen. Im Vergleich zu traditionellen Mischern, die sich auf langsames Rühren von Klingen verlassen, ist die Scherkraft weit entfernt. Der Hochschermischer kann in kürzerer Zeit einen empfindlicheren Mischeffekt erzielen, insbesondere für Emulgierung, Dispersion, Suspension und andere Prozesse. Der Hochschertempfleger kann den Mischzyklus erheblich verkürzen, die Produktionseffizienz sparen, Zeit und Kosten sparen und die Anforderungen an die hohe Produktionskapazität erfüllen. Bessere Gleichmäßigkeit und Stabilität Der Hochschermixer hat Vorteile des Fluid -Dynamikdesigns, das das Material vollständig scheren und gleichmäßig verteilen kann, wodurch das Problem des ungleichmäßigen Mischens vermieden wird, das durch traditionelle Mischung mit toten Ecken verursacht wird. Eine hohe Scherkraft fördert den vollen Kontakt zwischen kleinen Partikeln und Flüssigkeiten, um eine stabile Emulsion oder eine stabile Aufhängung zu bilden, und die Produktqualität ist hoch stabil. Wenn herkömmliche Mixer eine hohe Viskosität oder komplexe Formeln verarbeiten, sind Materialien anfällig für Schichten oder Agglomeration, was die Qualität des Endprodukts beeinflusst. Vieles Anwendungsbereich und flexible Prozesse Industrielle Hochschermischer eignen sich für eine Vielzahl von Materialien, von Flüssigkeiten mit niedriger Viskosität bis hin zu hohen Viskositätspfäfen, die effizient verarbeitet werden können. Die Ausrüstungsparameter sind einstellbar, und die Geschwindigkeit und der Spalt können entsprechend den Prozessanforderungen flexibel eingestellt werden, um die besonderen Anforderungen verschiedener Formeln für die Scherfestigkeit zu erfüllen. Traditionelle Mischer eignen sich meist für Materialien mit geringer Viskosität oder einfachem Mischen. Sie haben eine schlechte Anpassungsfähigkeit bei komplexen Prozessen, und ihre Effizienz und Auswirkung sind begrenzt. Offensichtliche Vorteile des Energieverbrauchs und der Betriebskosten Der Hochschertempfleger verfügt über ein optimiertes Design, eine hohe Scher -Effizienz und kann bei geringem Energieverbrauch ein effizientes Mischen erzielen. Durch variable Frequenzgeschwindigkeitsregulierung und intelligente Steuerungssysteme können Betriebsparameter in Echtzeit angepasst werden, um Energieabfälle zu vermeiden und die Produktionskosten zu senken. Traditionelle Mischer benötigen ein langfristiges kontinuierliches Rühren, haben einen hohen Strombedarf und einen geringen Effizienz sowie einen hohen Energieverbrauch, was es schwierig macht, die energiesparenden und Umweltschutzanforderungen der modernen Industrie zu erfüllen. Kompaktes strukturelles Design und bequeme Wartung Der Hochschermixer nimmt ein kompaktes Design an und belegt ein kleines Gebiet, das für Produktionsworkshops mit begrenztem Platz geeignet ist. Die Ausrüstung verfügt über eine gute Versiegelungsleistung, um Leckagen zu vermeiden und eine saubere Produktionsumgebung zu gewährleisten. In Bezug auf die Wartung sind der Laufrad und Stator des Hochschertempfehlers leicht zu zerkleinern und zu reinigen, die Ausfallzeiten zu verringern und die Produktionskontinuität zu verbessern. Die Struktur des herkömmlichen Mixers ist relativ einfach, aber es ist schwierig, Materialien mit hoher Viskosität zu reinigen, und der Wartungszyklus ist lang. Unterstützung diversifizierter Prozessanwendungen Industrielle Hochschermischer werden in vielen Branchen wie Pharmazeutika, Lebensmitteln, Chemikalien und Kosmetika häufig eingesetzt. Die hervorragende Emulgierung, Dispersion und Homogenisierungsfunktionen unterstützen die Produktion komplexer Formeln und gewährleisten die Gleichmäßigkeit und Stabilität von Produkten. Traditionelle Mixer erfüllen hauptsächlich einfache Mischanforderungen und sind schwierig, die modernen diversifizierten und qualitativ hochwertigen Prozessanforderungen zu erfüllen, die ihre Anwendungsbereiche einschränken. Reduzieren Sie das Risiko von Materialschäden Der Hochschertempfleger senkt zwar eine starke Scherung und reduziert das Material durch angemessenes Design mechanische Beschädigungen und eignet sich besonders für die Verarbeitung von Wirkstoffen und Biomaterialien, die empfindlich für Scherung sind. Traditionelle Mischer sind anfällig für Überhitzung und mechanisches Scheren, wenn sie lange mit hoher Geschwindigkeit gerührt werden, was zu einer Verringerung der Materialleistung und der Auswirkung der Produktqualität führt.
2025-07-07Als wichtige Mischungsausrüstung in der modernen Fertigung die Leistung von industrielle Hochschermischer Beeinflusst direkt die Produktqualität und die Produktionseffizienz. Unter vielen Parametern ist die Beziehung zwischen Fluss und Druck besonders wichtig. Ein tiefes Verständnis dieser Beziehung trägt dazu bei, den Betrieb der Geräte zu optimieren, die Prozesseffekte zu verbessern und somit reduzierte Produktionskosten und eine verbesserte Produktqualität zu erreichen. Einführung in das Arbeitsprinzip von Hochschermixern Hohe Schermischer bilden starke Scherkräfte zwischen hochgeschwindigen rotierenden Anprallern und Statoren, um Materialien schnell zu zerstreuen, emulgieren oder homogenisieren. Die Flüssigkeitsdynamikeigenschaften innerhalb der Geräte bestimmen die Wechselwirkung zwischen Fluss und Druck. Je höher die Laufradgeschwindigkeit, desto stärker die Scherkraft auf die Flüssigkeit im Statorspalt, was zu besseren Mischungseffekten führt und auch die Änderungen von Fluss und Druck beeinflusst. Grundlegende Beziehung zwischen Fluss und Druck Der Fluss bezieht sich auf das Materialvolumen des Mischers pro Zeiteinheit, der normalerweise in Kubikmeter pro Stunde (m³/h) gemessen wird; Der Druck bezieht sich auf den Druck auf das Material im Mischer, der im Allgemeinen in Pascals (PA) oder Balken exprimiert wird. Fluss und Druck zeigen eine bestimmte nichtlineare Beziehung. Unter konstanten Geschwindigkeits- und Ausrüstungsstrukturbedingungen steigt der Druck im Mischer in der Regel. Dies liegt daran, dass wenn mehr Material durch den schmalen Statorspalt führt, der Flüssigkeitswiderstand zunimmt, der Rückdruck erzeugt wird und der Druck entsprechend steigt. Der Druckanstieg ist jedoch nicht unbegrenzt, sondern durch Faktoren wie Laufradgeschwindigkeit, Spaltgröße und materielle Viskosität. Schlüsselfaktoren, die die Beziehung zwischen Fluss und Druck beeinflussen Laufradgeschwindigkeit Je höher die Laufradgeschwindigkeit, desto größer ist die Scherkraft auf der Flüssigkeit, desto höher ist die Flüssigkeitsflussgeschwindigkeit und desto höher der Durchflussausgang. Der Hochgeschwindigkeitsbetrieb führt jedoch auch zu einem höheren Druckerhöhung aufgrund einer erhöhten Flüssigkeitsbeständigkeit und Turbulenz. Stator- und Laufradlücke Die Größe der Lücke bestimmt den Raum, den die Flüssigkeit durchlaufen kann. Je kleiner die Lücke ist, desto größer ist der Widerstand gegen den Flüssigkeitsfluss, desto offensichtlicher ist der Druckanstieg und die Durchflussrate nimmt entsprechend ab. Das Einstellen der Lücke ist ein wirksames Mittel zur Steuerung von Fluss und Druck. Materialviskosität Materialien mit hoher Viskosität haben einen großen Strömungswiderstand, einen begrenzten Fluss und einen signifikant erhöhten Druck. Materialien mit niedriger Viskosität fließen reibungslos und haben einen niedrigeren Druck. Viskositätsänderungen haben einen signifikanten Einfluss auf die Strömungsdruckkurve. Systemwiderstand Der Widerstand von Rohrleitungen, Ventilen und anderen Geräten gegen die Flüssigkeit beeinflusst auch den Auslassdruck und den Fluss des Mixers. Wenn der Systemwiderstand groß ist, nimmt die Durchflussrate ab und der Druck steigt. Die praktische Bedeutung der Strömungsdruckkurve Die Flussdruckkurve spiegelt die Arbeitsleistung des Mixers wider. Die Kurve zeigt normalerweise einen negativen Korrelationstrend, dh desto höher der Druck, desto niedriger die Durchflussrate und umgekehrt. Das Verständnis dieser Beziehung trägt dazu bei, den optimalen Betriebspunkt der Geräte zu bestimmen und das Gleichgewicht zwischen Mischungseffekt und Energieverbrauch zu gewährleisten. Durch Anpassen der Geschwindigkeit und Lücke kann die Form der Kurve angepasst werden, um unterschiedliche Prozessanforderungen zu erfüllen. Eine angemessene Durchfluss- und Druckkonfiguration kann eine vollständige Scherung der Materialien erreichen und eine Heizungs- und Materialverschlechterung vermeiden, die durch übermäßiges Rühren verursacht wird. Technische Anwendung der Durchfluss- und Druckregulierung Industrielle Hochschermischer sind häufig mit variablen Frequenzgeschwindigkeitsregulatoren und einstellbaren Lückengeräten ausgestattet. Der Regler der variablen Frequenzgeschwindigkeit passt die Laufradgeschwindigkeit entsprechend den Prozessanforderungen an und steuert dynamisch den Strömung und den Druck. Das einstellbare Spaltgerät erreicht durch mechanische Einstellung eine präzise Steuerung der Scherintensität. Das intelligente Steuerungssystem kombiniert Sensordaten, um Druck und Fluss in Echtzeit zu überwachen, die Geräteparameter automatisch zu optimieren und die Produktionsstabilität und die Produktkonsistenz sicherzustellen. Diese Technologie verbessert nicht nur die Prozessgenauigkeit, sondern reduziert auch die Kosten für die manuelle Intervention erheblich.
2025-06-30Kontakt aufnehmen
Erfahrene Mitarbeiter und Experten stehen Ihnen jederzeit zur Verfügung, um Ihnen zufriedenstellende Produkte und professionelle Anleitungen zu technischen Problemlösungen zu liefern.